Fasteners and Machining: Important Elements for Precision Manufacturing
Fasteners and Machining: Important Elements for Precision Manufacturing
Blog Article
Browsing the World of Fasteners and Machining: Techniques for Precision and Rate
In the elaborate realm of fasteners and machining, the mission for precision and speed is a perpetual difficulty that requires careful interest to information and critical planning. From understanding the diverse variety of bolt kinds to picking optimum products that can withstand rigorous demands, each step in the procedure plays an essential function in accomplishing the wanted end result.
Understanding Bolt Kind
When selecting fasteners for a project, understanding the different types offered is important for making certain optimal efficiency and integrity. Fasteners are available in a large variety of types, each made for details applications and demands. Bolts are used with nuts to hold products together, while screws are versatile bolts that can be utilized with or without a nut, depending on the application. Nuts, on the various other hand, are inside threaded fasteners that friend with screws or bolts, giving a safe hold. Washers are essential for dispersing the load of the bolt and stopping damage to the product being secured. Additionally, rivets are irreversible fasteners that are perfect for applications where disassembly is not required. Comprehending the differences between these bolt types is important for choosing the right one for the work, guaranteeing that the link is strong, sturdy, and trusted. By choosing the ideal fastener kind, you can optimize the efficiency and longevity of your job - Fasteners and Machining.
Choosing the Right Products
Comprehending the relevance of choosing the right products is critical in ensuring the ideal performance and integrity of the selected bolt types talked about previously. When it comes to bolts and machining applications, the material option plays an essential function in determining the total strength, resilience, deterioration resistance, and compatibility with the desired setting. Different products supply differing buildings that can substantially impact the performance of the bolts.
Usual products utilized for bolts include steel, stainless steel, aluminum, titanium, and brass, each having its one-of-a-kind toughness and weak points. Steel is renowned for its high stamina and longevity, making it ideal for a vast array of applications. Stainless-steel uses exceptional rust resistance, ideal for environments prone to moisture and chemicals. Light weight aluminum is light-weight and corrosion-resistant, making it appropriate for applications where weight reduction is essential. Brass is frequently chosen for its visual charm and outstanding conductivity. Titanium is known for its outstanding strength-to-weight proportion, making it optimal for high-performance applications. Choosing the best material entails taking into consideration variables such as stamina requirements, environmental problems, and spending plan restrictions to guarantee the desired efficiency and durability of the bolts.
Accuracy Machining Techniques
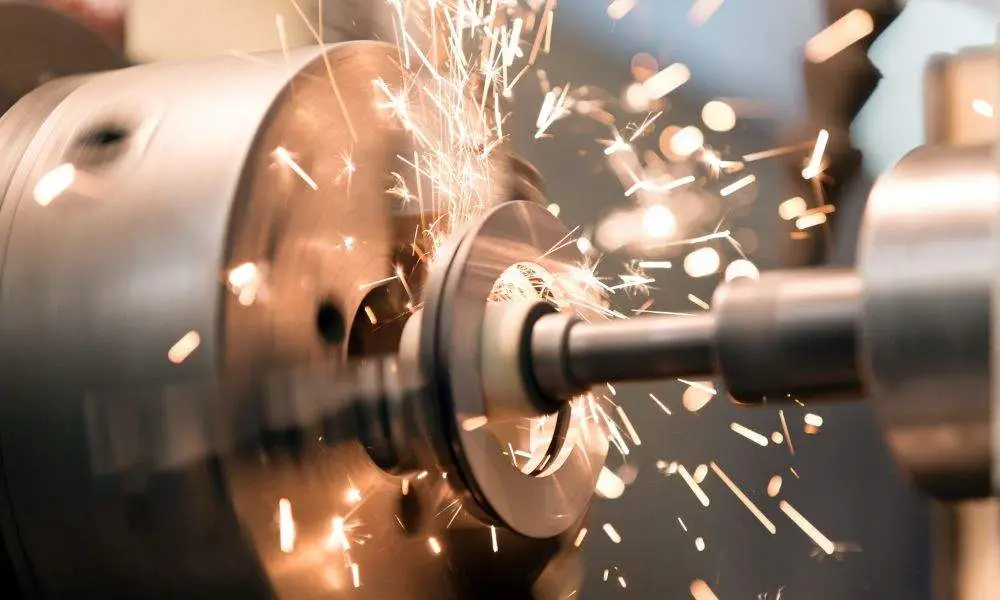
In enhancement to CNC machining, various other accuracy techniques like grinding, turning, milling, and drilling play crucial roles in fastener manufacturing. Grinding helps accomplish great surface coatings and limited dimensional tolerances, while turning is frequently utilized to develop cylindrical parts with accurate sizes. Milling and exploration operations are crucial for forming and developing holes in fasteners, guaranteeing they fulfill exact requirements and function correctly.
Enhancing Rate and Efficiency
To enhance bolt manufacturing procedures, it is vital to enhance procedures and implement effective strategies that match accuracy machining strategies. One key technique for improving rate and effectiveness is the execution of lean manufacturing principles. By minimizing waste and concentrating on continual improvement, lean methods aid enhance and eliminate bottlenecks workflow. Furthermore, buying automation innovations can significantly boost production speed. Automated systems can manage repeated jobs with precision and speed, enabling employees to concentrate on more complicated and value-added activities. Adopting Just-In-Time (JIT) inventory administration can also improve efficiency by guaranteeing that the right materials are available at the right time, minimizing excess supply and lowering preparations. Fostering a society of partnership and communication amongst team participants can improve overall performance by advertising transparency, analytic, and development. By combining these approaches, makers can achieve an equilibrium between rate and precision, inevitably enhancing their competitive side in the fastener sector.
Quality Control Actions
Executing rigorous high quality control actions is essential in ensuring the reliability and uniformity of bolt products in the production procedure. Quality control procedures incorporate different phases, beginning with the option of basic materials to the final assessment of the ended up fasteners. One essential facet of top quality control is conducting thorough product inspections to confirm conformity with specifications. This involves analyzing factors such as product composition, resilience, and stamina to assure that the bolts fulfill market requirements. Furthermore, keeping track of the machining processes is important to copyright dimensional accuracy and surface coating high quality. Using sophisticated technology, such as automatic examination systems and accuracy measuring devices, can boost the precision and effectiveness of quality assurance procedures.
Routine calibration of equipment and equipment is essential to keep uniformity in manufacturing and guarantee that fasteners fulfill the necessary resistances. Carrying out strict methods for determining and dealing with non-conformities or flaws is vital in protecting click here for more against substandard items from entering the market. By establishing a thorough quality control framework, suppliers can support the online reputation of their brand and deliver bolts that meet the greatest criteria of efficiency and resilience.
Conclusion
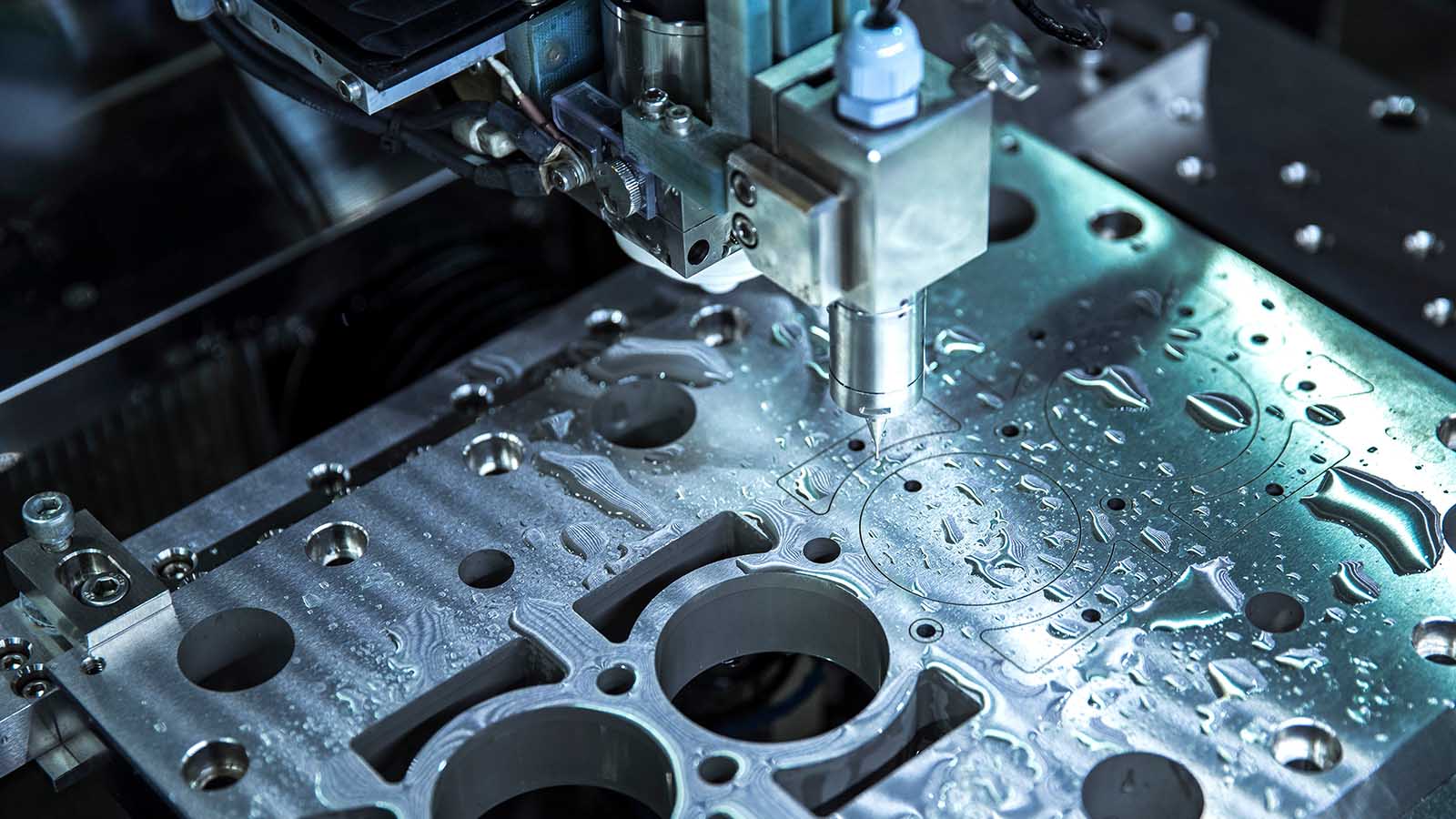
In the detailed world of bolts and machining, the pursuit for accuracy and rate is a continuous difficulty that demands careful interest to detail and tactical planning. When it comes to fasteners and machining applications, the material selection plays an essential role in identifying the overall strength, durability, corrosion resistance, and compatibility with the desired setting. Accuracy machining includes different sophisticated methods that ensure the limited resistances and specs required for fasteners.In enhancement to CNC machining, various other precision techniques like grinding, transforming, milling, and exploration play important functions in fastener manufacturing.To enhance fastener manufacturing procedures, pop over to this web-site it is vital to improve operations and apply effective techniques that match accuracy machining methods.
Report this page